For this installment of the Badger’s Den, I’d like to discuss WD-40.
But first, let me assure you: We are the same people delivering the same simple effective solutions as always. So if a web search brought you here looking for solutions for your muzzle loader, gun cabinet/safe storage & organizers, tool organization, etc. You are in the right place, and probably just a click or two away from finding it (try one of the links in the prior sentence), or try the menu in the side bar (if you are on a desktop computer… or scroll down if you are on your phone). Or just click here to go to Our Products.
But I hope you stick around and read my thoughts on WD-40.
What is WD-40? Now-a-days, that’s a tricky question. For many years, WD-40 was just the light oily stuff in a blue and yellow can that seemed to be on the shelf in every store. It got used on everything. And it got a bad reputation for drying out and leaving a cruddy crust that seemed to jam stuff up more than fix or lube it.
But now-a-days, WD-40 is still that same oily stuff in a can, and it’s a company, with an entire “WD-40 Specialist” product line. To keep it simple for this post, I’m going to address “Traditional WD40” as just “WD40.” The “WD-40 company” will be called “WD-40 company”. All the other “specialist” products the WD-40 Company sells, will be addressed by what I commonly call them: “WD-40 Dry lube” “WD-40 Corrosion Inhibitor” etc.
We don’t sell any WD-40 company products. But I use three of them, and you might too. Seeing they are available just about everywhere, effective when understood, and typically reasonably priced, it’s understandable that you’d have some on the shelf and use it. But the question is, are you using it correctly?
WD-40 actually does stack up ‘OK’ against many other products commonly used in automechanics: grime removal, rust penetrant, etc. It’s rarely the best, but it’s typically OK.
When it comes to guns, if you listen you will find lots of different opinions on WD40’s usefulness. Many will have horror stories, and tend to be negative. You probably heard stuff like: “Absolutely never use WD-40 on a gun.” If you did a little research you’d find statements claiming WD-40 products are in use in most gunsmithing schools. Can both be true? Is there more to this?
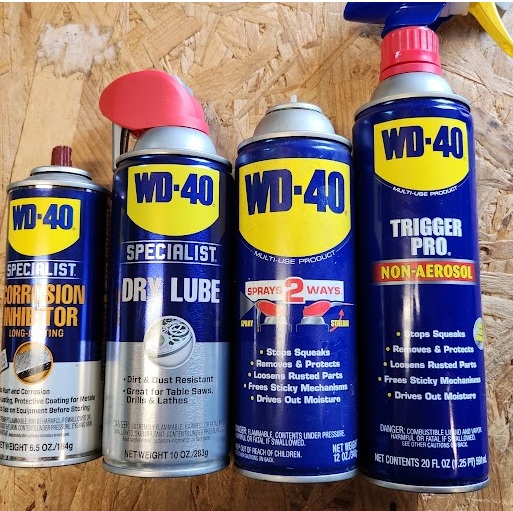
Let’s start our discussion with the Traditional WD-40. My understanding is that:
- WD-40 was formulated as a “Water Displacement” product while trying multiple formulations, and as it was the 40th formulation that was tried, it was named WD-40.
- The US Air Force was the largest of WD-40’s first purchasers. The USAF prescribed it as a metal treatment for it’s Titan Missiles. It was rubbed on the outer bare stainless steel skin to protect it from corrosion. On things like missiles, paint has weight and weight adds up. The missile can fly farther with a heavier payload the lighter it is, so they omitted paint and had the missileers rub them with WD-40.
- The Air Force guys got used to using WD-40 elsewhere and also seemed to be in the habit of bringing it home and using it on more stuff there. They wanted to buy it commercially, so it hit the shelves. It got used on all sorts of mechanisms, and became the ubiquitous can of lube on most folks shelves. WD-40 became so universal, that the company that made and sold WD-40 changed it’s name to “WD-40.”
- Please note: Traditional WD-40 wasn’t specifically designed as a lubricant, nor a penetrant. However it does seem to work pretty well in those regards… at least until the carrier evaporates and leaves a crusty crud that can jam up mechanisms.
So what does this mean for us gun owners? To me its pretty simple: I use WD-40 to clean crud off guns all the time. I find it especially useful in neglected black powder rifle bolts (something I work on regularly). If one of my guns takes a dip in the water, or hunts in the rain, I’ll hit it heavy with WD-40 too. But WD-40 is never the only thing, nor the last thing to touch one of my guns.
And again, I’m talking traditional WD-40 here. I see it as an effective, inexpensive way to remove moisture and heavy grime. Once that is gone, I remove the WD-40 with something else, and then lube and protect with a final more expensive product designed for the job: like gun oil (Rem-Oil, CLP, etc).
Don’t confuse WD-40 (traditional) with the Specialists. The “Specialists” are entirely different animals. Like WD-40 the “specialists” are reasonably priced, and readily available. They have specialized focuses. I use two of them daily, and pretty sure I have a third on the shelf somewhere. Mostly I use WD-40 Specialist Dry Lube. I use it often to remove the Traditional WD-40 I just doused something down with. The evaporative carrier in Dry Lube does a great job of carrying everything left behind away, and leaving it dry but lightly lubed with small PTFE balls. This dry lube feels slick, and leaves a surface that won’t attract dust, hold grime, and most of all doesn’t gel in the cold. I love to clean out shotgun magazine tubes with WD-40 Dry Lube and let it stay slick for feeding shells. Gun actions, trigger packs, and the interior of bolts get heavy doses of Dry Lube. The grime is allowed to float away. Then these mechanisms get drops of gun oil (Rem-oil/CLP) or small dabs of grease where needed.
Like it says on the Dry Lube can: this stuff works great on things like table saw blades, miter saw blades, and other stuff you want to keep dust free. I’ve seen a noticeable difference in how my saws cut after applying a little bit of it.
When I get metal that’s exposed or I need to store something and not worry about corrosion, I’ll hit it with WD-40 Specialist Corrosion Inhibitor. Frequently old antique guns that get stored more than shot, get cleaned, get whipped down with the WD-40 Specialist Corrosion Inhibitor, and then put away. The stuff is pretty greasy. So If I’m going to shoot a gun I coated with Specialist Corrosion Ihnibitor, I remove it and lube it properly with standard gun products. But that gun stays lightly coated with the Corrosion Inhibitor most of the time its in storage.
Small metal parts that I stock and sell get hit with Corrosion Inhibitor too. If you buy something from us, like Small Ruger Screws, they will arrive with a coating of this stuff.
The third one I have sitting around is Specialist Electric Contact cleaner. I’ve used it to blast gunk out of automotive electrical connectors & parts… just can’t find the can right now. Maybe I used it up and it’s time to buy another?
So is WD-40 good or bad? Well what WD-40 are you talking about? What is the application? I’d say WD-40 company products, are pretty good values, when you understand them and use them correctly. Like anything: if you want success, you need to be smarter than what you are operating. Start by reading the instructions!
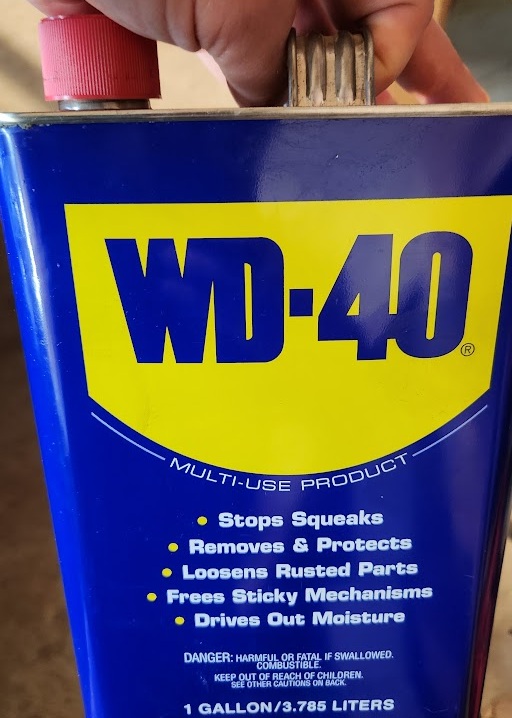
Are the Specialists the best at what they do? Maybe? The real question to ask is, “Are they effective enough and can you get your hands on them?” To me those are both “YES” answers, so I use them.
As a farewell, I’d like to point out that I rarely buy and use the aerosol version of Traditional WD-40. I get the “trigger pro” and refill it from gallon jugs. The can seems designed to prevent refills, so it does take some creative use of pliers, exacto knives, and funnels. I cannot find a more simple effective manner to clean all the grimy Remington 700 ML/MLS bolts sent to me. But those same bolts never leave with just Traditional WD-40 on them: its all Dry Lube, a drop of oil, and 3M molybdenum disulfide grease when they go.
Traditional WD-40 is never the only thing, nor last thing I use on any firearm component!